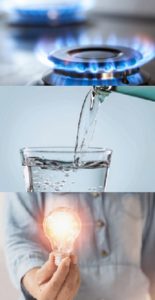
CLIENT
The fifth largest utilities company in US
KEY CHALLENGES
- Organization-wide data standardization initiative
- Replacement of several legacy systems with SAP
- Identifying supply chain challenges that occurred due to changes in business processes overtime, creating innovative solutions for such problems and their re-configuration in SAP system
- Improving erroneous inventory management and purchasing process resulting in multiple issues like duplication of supplier invoices, inability to track fuel consumption, fleet maintenance items and items in transit etc.
- Implementation of SAP WM, material serialization, Fleet Management and EAM modules
OUR SOLUTION
- Touchstone’s technical team implemented material serialization and scanning system for water meters, gas meters, back-flow preventers, valves, fire-hydrants and PVC and cross-linked polyethylene (PEX) pipes to automate and speed-up system entries that saved over 3000 man hours per year of manual entry work
- Identified items that were defined as stock items in some plants and non stock items in others causing item tracking issues that resulted in multi-million dollar losses over the period of several years
- Identified troublesome accounting entries unable to differentiate between material stock and consumption accounts
- Identified supplier payment duplication issues due to broken purchasing process
- This erroneous practice led the company to free-up multi-million dollars of blocked investment in dead inventories making a severely negative impact on company’s cash flow, operating cost, profitability in income statement and overall
- Set-up an effective material requirement planning (MRP) process
- Implemented an effective demand planning process for certain high consumption material
- Implemented ABC analysis to differential high, medium and low value stock items
As a result of an organization wide process improvement initiative
- Stock items and non stock items were clearly defined and categorized, significantly reducing the number of items in item master
- Material master data and material master records were standardized
- Data standardization and uniform processes were implemented across all plants
- This improvement initiative enabled the company to establish efficient processes for S&OP, demand planning, and material requirement planning resulting in an immediate annual profit of $7 million
- $9 million of additional revenue was generated in that particular financial year by identifying and utilizing the dead stock of several items