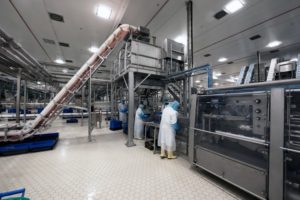
CLIENT
Midsize meat plant equipment and tools manufacturing Co. In Midwest
KEY CHALLENGES
This client was in a transition phase of growing from a small manufacturing firm to a mid size manufacturing organization that was engaged in the manufacturing of equipment and tools used in meat plants and food processing industry. This client had a small IT department and ran operations on proprietary software applications, small home grown programs and spread sheets. With the exponentially growing business, client outgrew its IT applications landscape and it became increasingly challenging for the client to run the operations on daily basis making the business decision making process extremely time consuming for the top management and eventually resulting in a high level of customer dissatisfaction. Client sought Touchstone’s help for an effective solution.
OUR SOLUTION
Touchstone suggested the client to implement SAP BusinessOne and carried out the full life cycle implementation which resulted in:
- Adoption of Industry best practices in all areas of business
- Improved, optimized and standardized business processes across the organization
- A total data cleansing of master and transaction data and standardizing data
- Migration of data from several legacy systems to centralized SAP Business One application resulting in a tremendous reduction of data redundancy
- Seamlessly integrated departments and business processes led to significantly reducing the time consumption on daily operations resulting in higher level productivity, employee moral, better transparency across the departments leading to higher customer satisfaction and improved supplier relations
- Real time reports assisting the top management in rapid decision making process providing company a competitive edge in the marketplace
- Well trained, well informed and highly motivated employees were able to take more responsibilities and delegated more authorities reducing the need of “approval” process saving hundreds of hours a year
- Streamlines MRP process led to tremendous reduction in inventory, and dead stock speeding up “make or buy” decisions significantly increasing the profits
- Uninterrupted production process resulted in reducing the cost of labor, cost of sales lost, and cost of discounts from suppliers lost adding to the increased profits
- Streamlined accounting resulted in the reduction of cost of audit
- A high level of collaboration between purchasing, inventory, production, customer service and sales teams resulted in a well coordinated business operations and exponential increase in sales