Game On – Reduce Time, Increase Efficiency And Strengthen Strategic Decisions With Our EPM Solution
Game On – Reduce Time, Increase Efficiency And Strengthen Strategic Decisions With Our EPM Solution
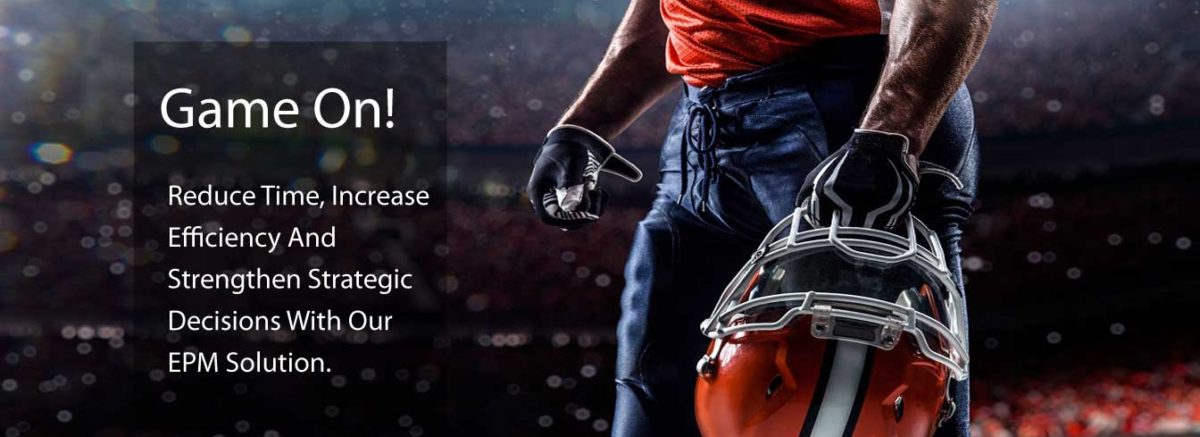
Game On – Reduce Time, Increase Efficiency And Strengthen Strategic Decisions With Our EPM Solution
Reinvent – Your Business and Unveil New Opportunities With Advance Analytics & Data-driven Insights
Transform – Into A NextGen Enterprise With Touchstone’s Digital Transformation Technology Offering
Conquer – Your Challenges With Our Innovative Technology Solutions & Management Consulting Services
Evolve – Into a Supply Chain Powerhouse With Touchstone’s Best-in-Class Supply Chain Strategy Consulting
Thrive – Our Corporate Strategy, Turnaround & Transformation Advisory Is Meant To Do Just That
So here is the process flow within the APO system and how APO works: The fundamental problem of Supply Chain Planning is that the delivery time of products to customers is supposed to be substantially shorter than production time or lead time. In order to be able to realize a short delivery time, a pre-planning procedure is carried out that …
SAP APO can be integrated with both ECC and non ECC systems. Integration between SAP APO and ECC system takes place via CIF while its integration with non SAP systems takes place through BAPIs (Business Application Programming Interfaces). CIF is a real time interface that can integrate APO with multiple ECC systems. Only the data objects needed in the data …
SAP Production Planning consists of the following: Master Data – includes the material master, work centers, routings and bill of materials. S&OP – Sales and Operations Planning (SOP) provides the ability to forecast sales and production plans based on historical, current and future data. DRP – Distribution Resource Planning allows companies the ability to plan the demand for distribution centers. …
For planning purpose, some master data and transaction data from Materials Management- Purchase module is required to be transferred from ECC system to APO system. First let’s see how the data flows in Procure-to-Pay (PTP) cycle in SAP Materials Management and what all master data and transaction data is created in Purchase process: Purchase process flow: Determination of requirement Stock …
Supply Chain Management process starts in ECC with Sales & Distribution. First of all sales orders are created in ECC system and then they are transferred to SCM where Demand Planning converts them to planned independent requirement. Sales & Distribution process flow follows the steps, sub-steps and transaction codes as below: SAP SD Order To Cash Transaction Codes Create Material …
In SAP, Supply Chain process is categorized into three different sub-processes- Supply Chain Planning Supply Chain Execution Supply Chain Collaboration These three sub-processes further cover the following areas in SAP: Here is a brief description of all the three areas in SAP’s own language: Supply Chain Planning: Supply Chain Execution: Supply Chain Collaboration: As I mentioned …
Material Requirement Planning (MRP-I): The concept of MRP (MRP-I) was developed in 1970s to assist the manufacturing firms efficiently manage their material procurement process in order to support their production operations in a much better way. Let’s go back to Collaborative Supply Chain – II; diagram no. 3, MRP translates the independent demand (top level assembly) of MPS into component …
MASTER PRODUCTION SCHEDULE Master production schedule is a master level or top level schedule used to set the production plan in a manufacturing facility. It is usually a medium-term production plan indicating the start of manufacturing in quantities and lead times for each article according to demand and the company’s capacity. The MPS is used in particular to establish the …
Since it is not possible to explain each and every supply chain management term in this blog, I have picked some most frequently used terms to explain here. Some of these terms can be very well understood just in few lines of explanation and I have explained them on this page but few terms I would like to explain in …
Theory of constraint (TOC) is based on the dictum- “A chain is only as strong as its weakest link”. Theory of constraint was propounded by Dr. Eliyahu M. Goldratt and was published in his book “The Goal” in 1984. Theory of constraint is a management paradigm that views any manageable system as being limited in achieving more of its goals …
Bandwagon effect is a psychological phenomenon whereby people do something primarily because other people are doing it, regardless of their own beliefs, which they may ignore or override. The bandwagon effect has wide implications, but is commonly seen in consumer behavior. For example, people might buy a new electronic item because of its popularity, regardless of whether they need it, can …
Gerard P. Cachon (Fred R. Sullivan professor of operations and information management-The Wharton School) defines bullwhip effect as – “The phenomenon of increasing demand variability in the supply chain from down stream echelons (retail) to upstream echelons (manufacturing).” Bullwhip effect is more common in forecast driven supply chain and suggests that the variation in demand increases up the supply chain …
Forecasts are developed for a company’s finished goods, components and service parts. The forecast is used by the production team to develop production or purchase order triggers, quantities and safety stock levels. Forecasts are highly dynamic in nature and need to be reviewed by management on a regular basis. Failing to maintain an accurate demand forecast can result in a …
Demand forecasting, sometimes also referred as sales forecasting and demand planning, is the first and the most crucial step of a supply chain planning process. Level of accuracy in sales forecasting and effectiveness of demand planning in an organization determines how efficient and successful the company’s supply chain is going to be. In sales forecasting process, sales and marketing department …
Before one gets into a more detailed discussion about various Supply Chain strategies such as Purchasing Strategies, Inventory Strategies, Production Strategies, Warehousing Strategies, etc. and discuss some real life cases, one needs to understand some basic supply chain terms and concepts. Since I have already explained few things like SCOR, DCOR, CCOR, KPIs, Performance metrics, Oliver Wight checklist, Balance Scorecard, …
I have tried my best to sequentially depict the high level process flow of entire Supply Chain process in the following process flow diagrams which is self explanatory and describes the processes and their sequence right from your suppliers to your customers. Also you may want to download a more detailed Supply Chain process flow from this download link: Internal …
As we learnt in Customer’s EVA, customer is the sole focus and the only cause why any organization would love to optimize its supply chain. It serves two purposes: First is, obviously, going beyond the customer’s expectations in terms of availability of “Right Product at the Right Price, at the Right Time and at the Right Location”. Second, maximizing value …
The prime determinant of your company’s supply chain metrics is the level of your understanding about how your supply chain impacts your customers, and specifically how it impacts a customer’s EVA (Economic Value Added). EVA is a true measurement of the financial health of a company’s supply chain. This is based on the principle that a company’s financial health is …
One of my favorite books on Business Process Improvement is Oliver Wight Class A Checklist For Business Excellence Sixth Edition. Oliver Wight’s Class A Checklist is the accumulated practice and experience of Oliver Wight Consultants around the world. It reflects the effort and achievement of thousands of client companies who have used this checklist standards to make a difference in …
Integrated Supply Chain Framework (DCOR-SCOR-CCOR) With relatively maturing Supply Chain practices and increasing competitive environment, companies are now striving to get the maximum value return out of their supply chain investment. In order to improve, streamline and standardize the business processes across the entire supply chain, more and more companies are adopting the Integrated Supply Chain framework (DCOR-SCOR-CCOR) by concatenating …
Unlike the traditional performance measures which focus on only the financial throughput and monetary output of the supply chain, Balanced Scorecard provides the organizations with much more balanced overall business performance perspective by focusing on four different performance measures: Financial Growth Customer Quality through Business Process Improvement Innovation, Learning and Growth Scorecard must be aligned to the organization’s vision and …
Supply chain metrics are the measurements to track and evaluate supply chain performance. It enhances our understanding about how our supply chain is operating and performing over a period of time. One thing that everyone needs to understand is that merely having a scale of measurement is not the solution to the gray areas, the real solution is developing a …
A KPI Scorecard is a specific application of a scorecard which is used to measure progress toward a given set of KPIs and minimize the gap between the KPIs and Benchmarks. It adds value to the organization by connecting KPIs within tactical and operational levels in an organization to the overall strategy of the organization. Scorecards can be implemented at …
Supply Chain Operations Reference model (SCOR) model was first propounded by Supply Chain Council (SCC) in 1996. The Supply Chain Council now has closer to 1,000 corporate members worldwide and has established international chapters in North America, Europe, Greater China, Japan, Australia/New Zealand, South East Asia, Brazil and Southern Africa. Supply Chain Council’s membership consists primarily of practitioners representing a …
Supply chain decisions can be categorized into two categories: Temporal Decisions Functional Decisions A. TEMPORAL DECISIONS: Temporal decisions can be classified into three categories: strategic, tactical, and operational according to the time horizon of the decisions. Strategic decisions are made on Organizational level and focus on long term objectives of a supply chain and guide the supply chain policies from …
Supply Chain Management is a seamless concatenation of various supply chain entities, activities and other components leading to the smooth run of sourcing, production and logistics functions and resulting in delivery of products or services at the right time, right place and for a right price. A well managed supply chain is a great strategic as well as competitive advantage …
Supply chain encompasses everything from determining the source of the materials, procuring the materials, warehousing the materials, producing the finished goods, warehousing the finished goods, determining the means of transportation and transportation routes, distributing goods to distribution centers/channel partners/end customers as well as the system required to run these operations in a perfect coordination. A supply chain can also be …
My passion for Supply Chain Management and love for technology have long been encouraging me to start this blog. I always promised myself to initiate this wonderful blog one day but after a long series of procrastinations, today I am finally initiating “SCMChamp: A Supply Chain Management Blog”. Every time I go to a store and buy a packet of …